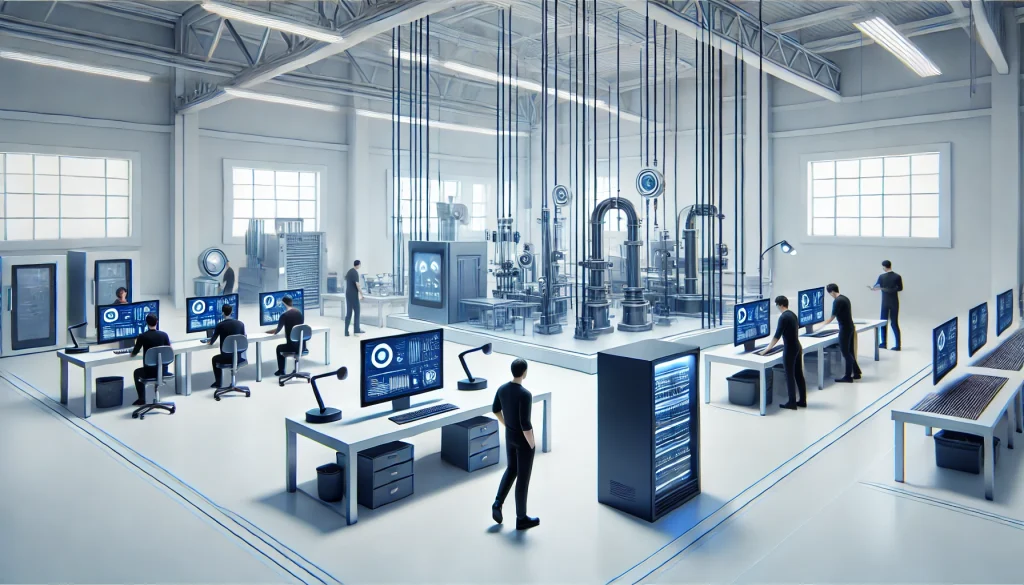
Have you ever walked into a factory where technology feels like a friend, not a frustrating puzzle? That’s the power of digital accessibility in manufacturing. It helps create tools and interfaces that actually work for the people using them.
Think about it: Why should complex machinery be hard to understand? Why should workers struggle with interfaces that seem designed to confuse? Digital accessibility breaks down these barriers, making technology simple, intuitive, and truly helpful.
Let’s understand why this matters and how it can transform manufacturing for the better:
1. Enhancing Efficiency and Reducing Errors
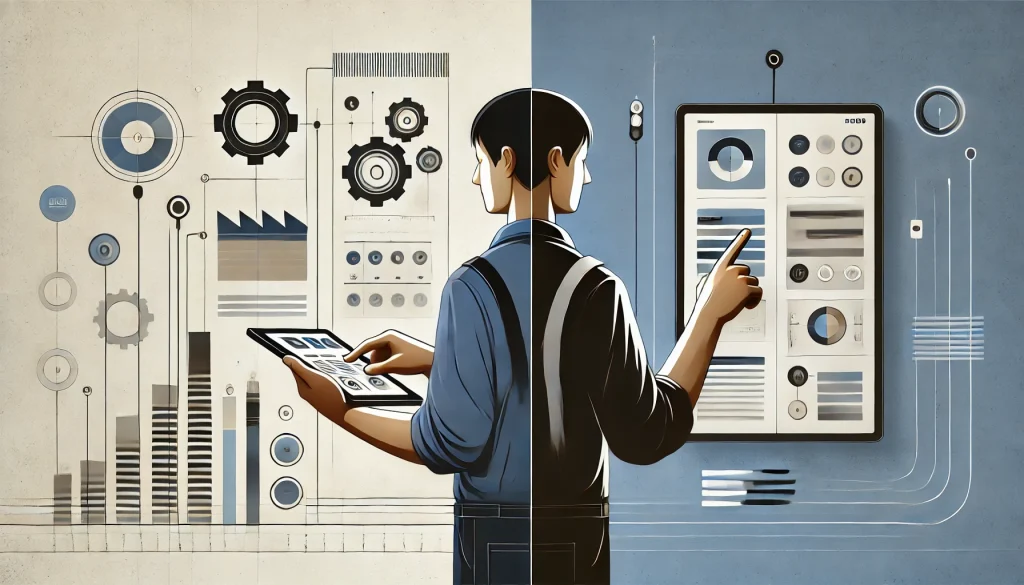
Factory workers rely on digital interfaces to operate machinery, track production data, and follow workflows. When these interfaces are not accessible, employees with disabilities—or even those who are not tech-savvy — face difficulties that slow down production and increase the risk of errors.
By implementing accessible UX designs, manufacturers can improve operational efficiency. Features like voice commands, screen readers, and intuitive UI design help workers navigate complex systems effortlessly. According to studies, 87% of organizations that implemented digital accessibility measures saw improved user experience across the board.
2. Addressing the Manufacturing Skills Gap
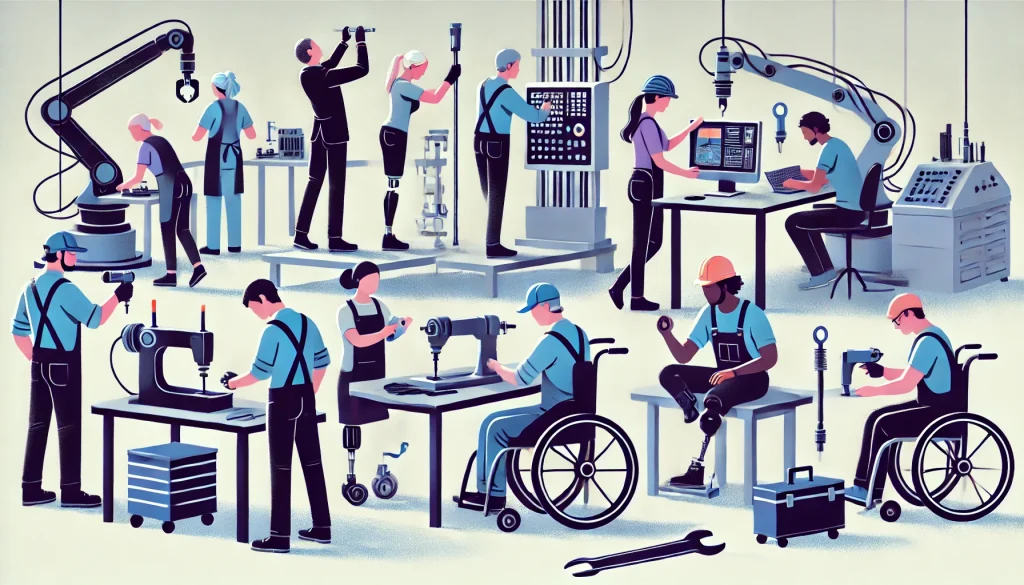
The manufacturing industry is facing a massive skills gap. Deloitte estimates that 2.4 million manufacturing jobs in the U.S. could go unfilled by 2028 due to a lack of skilled workers. One way to bridge this gap? Hiring people with disabilities who are often overlooked but bring valuable skills to the workforce.
Making digital tools accessible means opening doors for a more diverse talent pool. When workers can easily interact with machinery, software, and safety protocols regardless of their physical abilities, manufacturers can tap into a broader workforce and help alleviate labor shortages.
3. Improving Workplace Safety
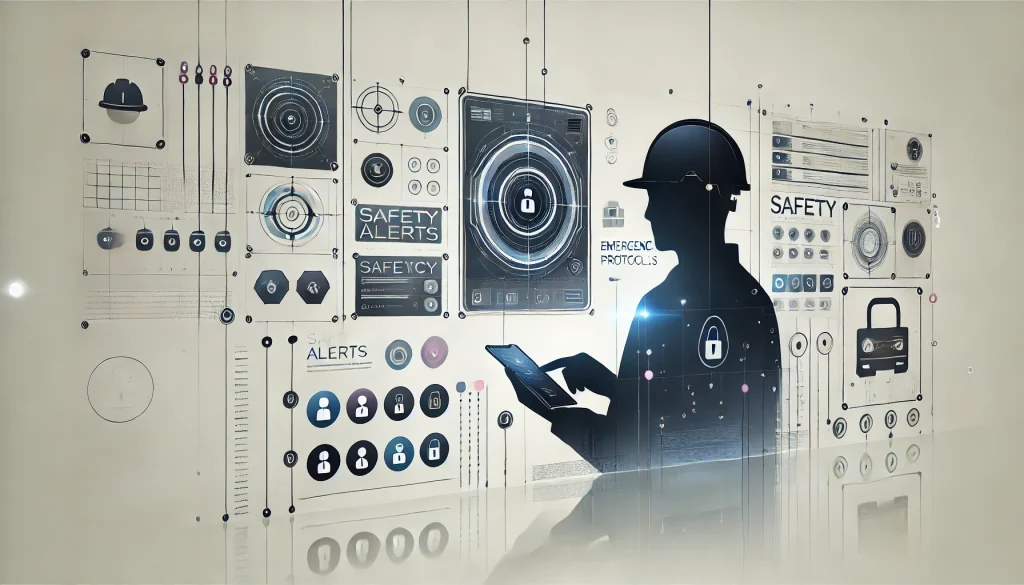
Safety is paramount in manufacturing. Workers need to access real-time alerts, equipment controls, and emergency protocols without barriers. Accessible digital interfaces ensure that information is clear, readable, and available in multiple formats — visual, auditory, and tactile.
For example, using high-contrast displays, large font sizes, and audible alerts can help workers with visual impairments stay informed.
4. Avoiding Legal Risks and Compliance Issues
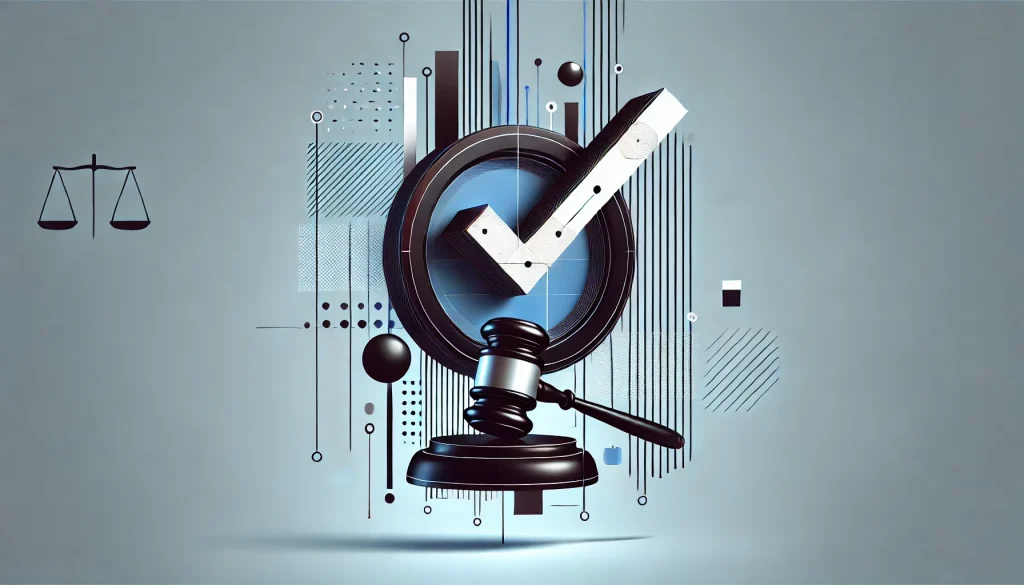
Ignoring digital accessibility can be costly. In 2023, 4,605 web accessibility lawsuits were filed, reflecting a 42% increase from 2022. This upward trend has persisted into the first half of 2024, with many cases targeting companies whose digital platforms fail to meet accessibility standards.
Manufacturing companies that neglect accessibility could face legal challenges under the Americans with Disabilities Act (ADA) and similar global regulations.
By proactively designing accessible digital interfaces, manufacturers can avoid legal pitfalls, improve compliance, and protect their brand reputation.
5. Boosting Employee Morale and Productivity
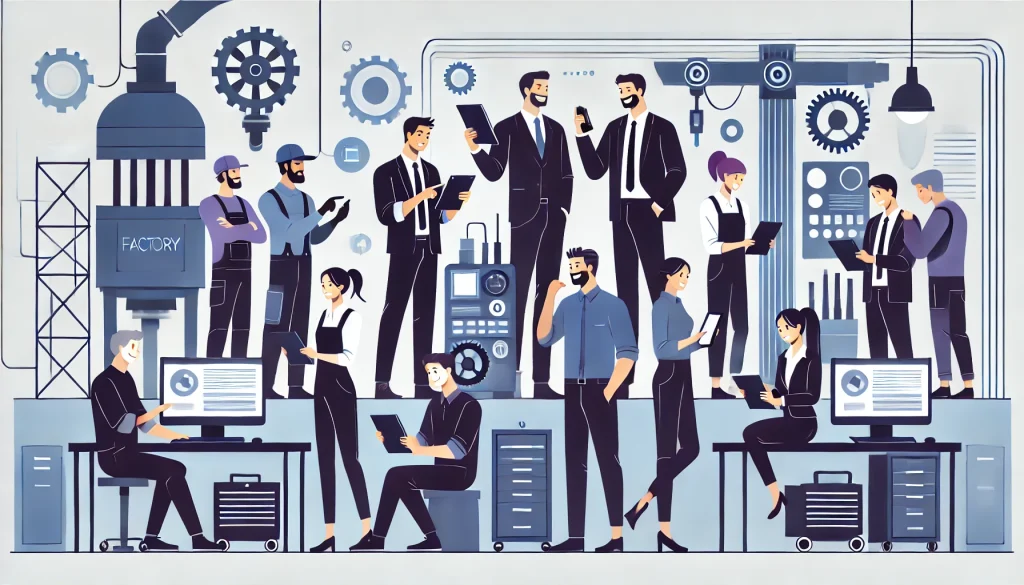
An inclusive workplace fosters a positive work culture. When factory workers feel valued and supported, their job satisfaction and productivity rise.
A well-designed, accessible digital experience eliminates frustration and enables workers to focus on their tasks rather than struggling with poorly designed systems. This, in turn, boosts overall efficiency and morale.
How to Implement Digital Accessibility in Manufacturing
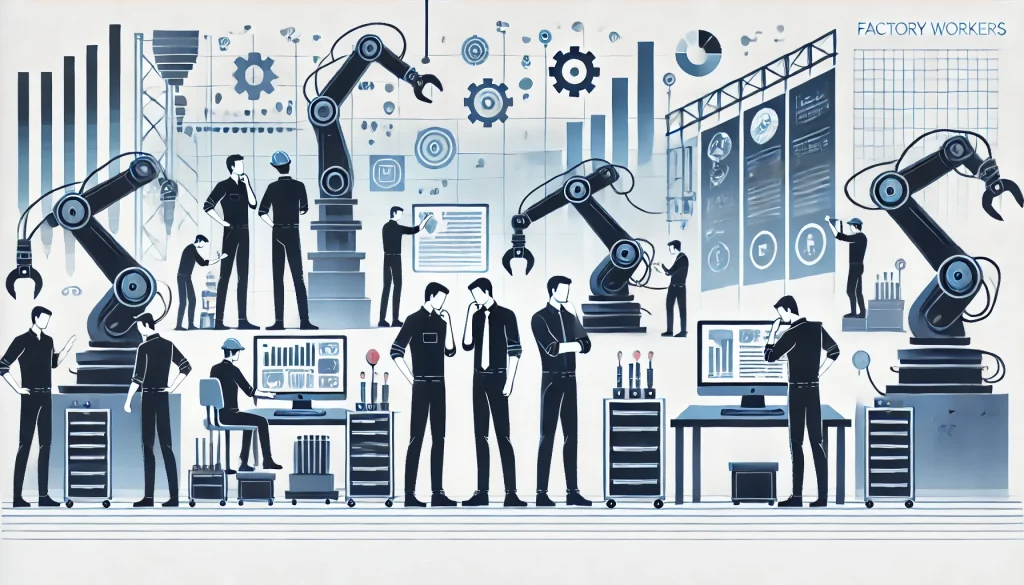
So, how can manufacturing companies make their digital UX more accessible? Here are some key steps:
a. Conduct Accessibility Audits
Regularly evaluate digital tools, interfaces, and processes to identify and fix accessibility barriers. This includes assessing machine interfaces, control panels, and software to ensure they support users with different abilities.
b. Use Inclusive Design Principles
Ensure that all digital interfaces, from production floor dashboards to enterprise resource planning (ERP) systems, are designed with accessibility in mind. Use high-contrast visuals, scalable text, and intuitive navigation that accommodates different user needs.
c. Invest in Assistive Technology
Implement assistive features such as voice-controlled interfaces for hands-free operation, magnifiers for better screen visibility, and screen readers for visually impaired employees. Additionally, consider adaptive input devices like one-handed keyboards or eye-tracking software for workers with mobility impairments.
d. Provide Employee Training
Accessibility isn’t just about technology — it’s also about how employees use it. Conduct training sessions to familiarise workers with accessibility tools and best practices. Educate both employees and supervisors on how to create an inclusive work environment.
e. Encourage a Culture of Inclusion
Digital accessibility should be a core part of a company’s culture. This means establishing clear accessibility policies, gathering feedback from employees with disabilities, and involving them in the design and testing of digital tools. Leadership should champion accessibility initiatives and integrate them into the company’s broader digital transformation strategy.
Challenges in Implementing Digital Accessibility & How to Overcome Them
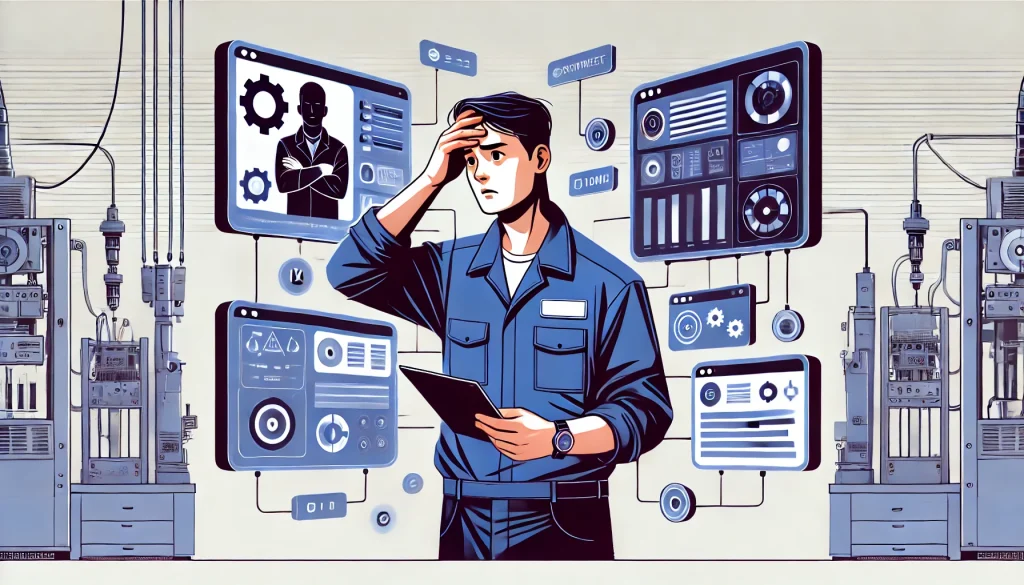
Despite its benefits, integrating accessibility into manufacturing UX comes with challenges. Here’s a look at common obstacles and how to address them:
➝ Legacy Systems: Many manufacturing plants still use outdated systems that are not designed with accessibility in mind.
Solution: Conduct an accessibility audit and gradually upgrade legacy systems to ensure compatibility with assistive technologies.
➝ Lack of Awareness: Many decision-makers are unaware of the need for accessibility and its business advantages.
Solution: Educate leadership and employees on the importance of accessibility and provide training on best practices.
➝ High Initial Investment: Implementing accessible digital solutions may require upfront costs in technology upgrades and training.
Solution: Utilise government incentives, grants, and tax benefits available for businesses that implement accessibility improvements.
➝ Resistance to Change: Employees and management may resist new technologies and processes.
Solution: Engage with accessibility experts to ensure a smooth transition and demonstrate how inclusive technology benefits everyone.
Key Trends in Digital Accessibility for Manufacturing

- AI-Powered Assistive Technologies: AI-driven tools, such as voice assistants and smart glasses, are making factory environments more accessible.
- Wearable Technology: Smart gloves and exoskeletons help workers with mobility impairments perform tasks more efficiently.
- Augmented Reality (AR) and Virtual Reality (VR): AR/VR training programs make learning more accessible to individuals with different learning abilities.
- Cloud-Based Solutions: Cloud technology enables workers to access information remotely, improving accessibility for all employees.
Conclusion
The future of manufacturing belongs to companies that understand one simple truth: technology should serve people, not the other way around. When we design with empathy, accessibility becomes more than a feature — it becomes a powerful catalyst for human potential.
Also Read: Why Accessibility in Insurtech Isn’t Just an Option – It’s Essential!